СООБЩЕНИЕ
В связи с обилием коллцентров и других коммуникационных услуг ОБРАЩАЕМ ВАШЕ ВНИМАНИЕ, что у нас нет диллеров и коллцентров, поэтому общение с Вами ведут непосредственно исполнители ваших заказов - инженеры.
Названные цены, сроки и параметры работ не будут "взяты с потолка".
Все фотографии наши, на нашем оборудовании, сделанные нами.
3D печать в производстве обуви
Приводим Вам два положительных примера использования 3D-принтеров, компаниями, занимающимися производством обуви
компания Timberland 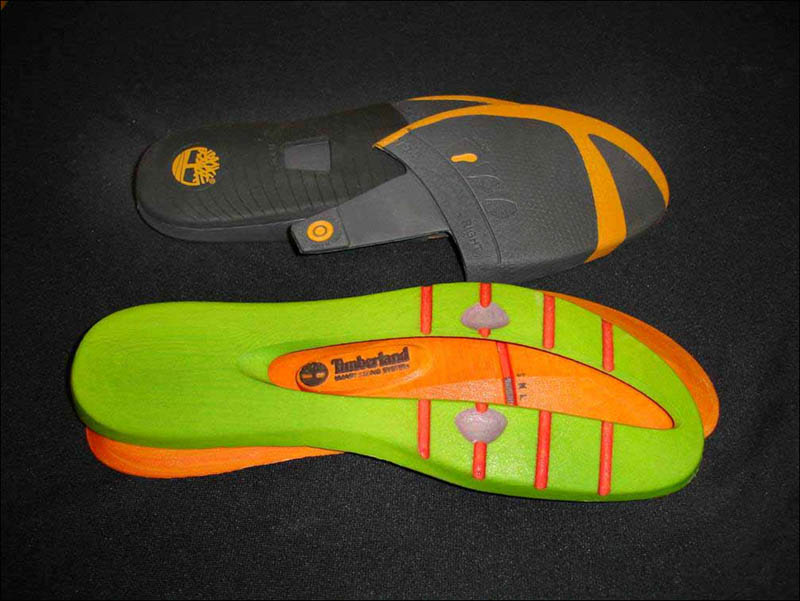
Сделать лучше. Именно такой лозунг использует компания Timberland, обувь которой известна своей прочностью и качеством. Акцент на тонкую, изящную работу не должен вызывать удивления, так как компания была основана мастером строчильной машины, очень любившим свою работу и гордившимся ей. Растущая на $1,6 млрд. за год глобально по всему миру («Ежегодный отчет компании Timberland за 2005 год», www.timberland.com), Timberland сегодня имеет в штате армию дизайнеров существенных размеров для постоянного совершенствования своей продукции: общей формы, подошвы, ортопедических устройств; такой подход обеспечивает наилучший результат для любителей приключений и альпинистов, которые полагаются на свою обувь.
Четыре года назад, мастера Timberland для создания профессиональной модели использовали прототипы на ранней стадии разработки из дерева или вспененного пластика, основанные на 2D чертежах. Стоимость каждого прототипа составляла примерно $1200, для изготовления прототипа тратилось времени около недели. Относительно высокая стоимость и низкая скорость воспроизведения замедляли процесс разработки.
Однако, в конечном итоге, компания была ознакомлена с технологией быстрого прототипирования. Затратив шесть месяцев на сравнительный анализ технологий, имеющихся на рынке, Timberland купили принтер ZPrinter 310. В 2005 году Timberland перешли к более новой версии оборудования для прототипирования, принтеру Spectrum 510 от Z Corporation, способ-ному печатать 24-битный цвет с разрешением 600 точек на дюйм. Сейчас требуется лишь 90 минут для того, чтобы изготовить прототип в цвете, имеющийся в идее дизайнера. Стоимость каждой модели составляет около $35. «Теперь мы можем быстро сделать бесчисленное количество итераций и вариаций»,—замечает Тоби Рингдэйл, IT директор отдела разработок.— «Конструкторы и менеджеры по маркетингу могут действительно знать, как будет выглядеть их продукт и быть уверены, что он соответствует требованиям потребителей».Высокое разрешение и цвет позволяют выявить критические моменты в дизайне на прототипе, например, окончание подошвы и скорость зацепления верхней части. Прототип дает менеджерам по продажам Timberland преимущество над своими конкурентами, которые ограничены серией 2D чертежей и 3D изображением, часто без преимуществ раскраски цветом. «В нашей отрасли всегда важно быстро, в соответствии с возможностями покупателя, реагировать на тенденции рынка и предпочтения покупателя, что демонстрирует положительный настрой»,—говорит Рингдэйл.—«Принетры Zcorp делают это за нас, снижая время и затраты на разработку новой модели, помогают нам делать обувь лучше для наших покупателей».
компания Converse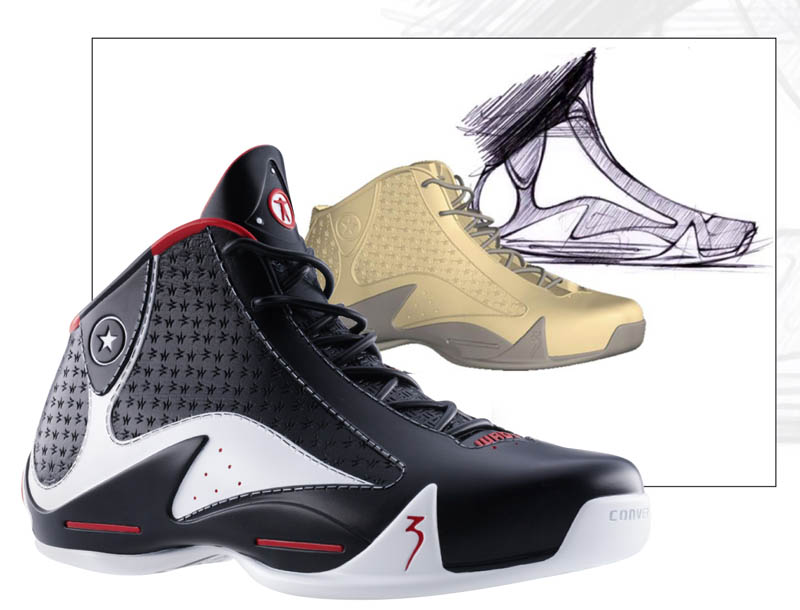
В принципах разработки продукции компании Converse с появлением трехмерного принтинга произошла технологическая революция.
Компания Converse - ведущий производитель спортивной обуви. Брайан Киофи (Bryan Cioffi) работает в компании менеджером по созданию цифровой продукции. В прошлом
Брайан работал в фирме биомедицинских разработок, где руководил группой специалистов и познакомился с технологиями быстрого моделирования.
Затем, когда Киофи пришел в компанию Converse, он вскоре выяснил, что здесь отсутствует возможность быстрого моделирования, «и очень захотел организовать работу в этом направлении». Киофи говорит, что до того, как он внедрил трехмерный принтинг в компании Converse, обувь там делалась тем же способом, что и в прошлом столетии. Дизайнеры и разработчики сначала делали наброски компонентов, а затем отправляли их в Азию. Там эти наброски попадали в руки модельщику, который по ним вырезал детали, а затем делался так называемый макет. Фотографии макета отсылались назад в США для окончательной доводки модели. Частенько дизайнерам нужно было летать в Азию, чтобы проверить, как идет дело с изготовлением спроектированной ими обуви. В ходе каждой проверки обувь разбиралась на части, а потом опять сшивалась. Весь этот процесс занимал 3-4 недели
Полный цикл от разработки до выпуска продукции мог занимать месяцы - в основном, из-за пересылки компонентов туда-сюда до их окончательной доработки. «Это было нелепо» -добавляет Брайан.
По настоянию Киофи компания Converse приобрела ЗD-принтеры, изготавливающие модели из полимера ABS, и т.н. «струйные» 3D-принтеры (технология «inkjet»). Последние, по словам Брайана, особенно ему понравились, так как позволяли изготавливать многоцветные модели.
Более того, спустя несколько месяцев, «струйный» принтер показал свое несомненное преимущество перед ABS-принтером. «Иногда я пытался сделать одинаковые части на обеих машинах, однако ABS-принтер действовал смехотворно медленно. Принтер работал всю ночь, а я приходил и обнаруживал, что сделан лишь небольшой фрагмент детали» - вспоминает Киофи. Брайан Киофи начинал с изготовления малого числа отдельных компонентов, но теперь делает обувь «целиком, от начала до конца». Как только дизайнеры из США дали «добро», такие же трехмерные модели стали делать в Азии и использовать для изготовления моделей и форм. В результате значительно сократились издержки и время выхода новой продукции на рынок.
«Теперь мы можем делать пять полностью законченных моделей обуви за 10 часов. Когда использовался ABS-принтер, на одну модель уходило 55 часов.» В результате ABS-принтер был продан - для того, чтобы приобрести другой, более совершенный «цветной» Зй-принтер. Учитывая, что трехмерные принтеры отлично себя зарекомендовали, компания Converse недавно приобрела
ZPrinter650® для главного офиса в Массачусетсе
и трехмерные принтеры других марок для офисов в Коста-Меса (Калифорния) и Азии.
Киофи замечает, что у компании появилась возможность резко сократить число сотрудников, каждый год бывающих в Азии (каждый из них обходится фирме в 10 - 12 тысяч долларов). «В прошлом году расходные материалы для нашего принтера обошлись бюджету в сумму всего около 30 000 долларов, но, возможно, мы сэкономили средства на 8 поездках в Азию. Это оправдывает себя» - говорит Брайан.
Далее он замечает - «Мы видим невероятное снижение затрат на инструмент - от 350 000 долларов в 2006 году до всего 150 000 долларов в 2008 году».
«Мы работаем с уникальной разноцветной обувью и с помощью ЗD-принтеров корпорации Z Corporation мы имеем потрясающе великолепный цвет. Вот так эти машины изменили способ производства - теперь мы можем даже принимать заказ на выпуск продукции по телефону».
Статья подготовлена по материалам журнала Cadalist и фирмы ZCorp